Shell-solid hybrid bracket
Transitioning from thick, bulky areas to thin ribs can be done in several ways, one of which is represented in this section. The part in the pictures is modeled with tetra solid elements where the thickness is exceedingly thick compared to the element length, and the ribs which have a much smaller thickness are represented as shells. The biggest challenge and also the point where we excel in the process of building up this type of components, is connecting together the shell and tetra solid regions. This merging/blending interface is sometimes difficult to model due to the lack of clean transition areas/ feature shapes.
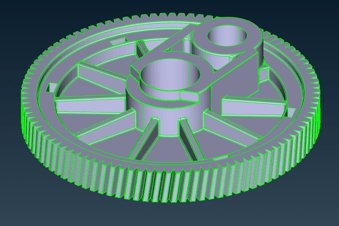
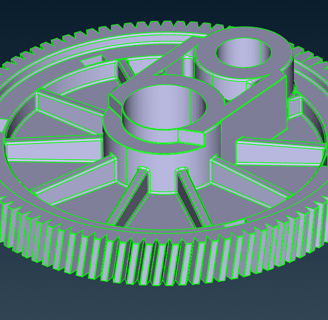
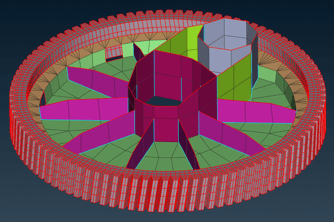
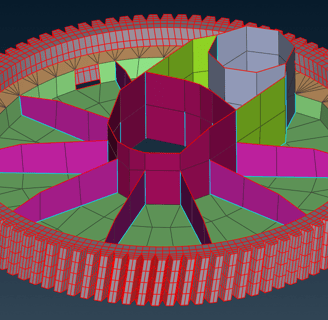
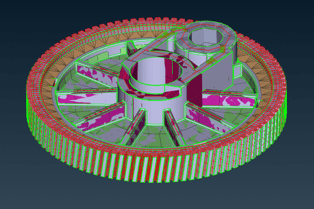
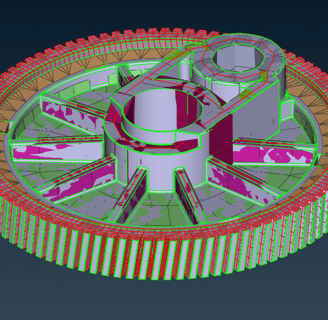
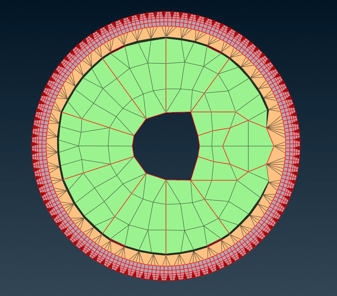
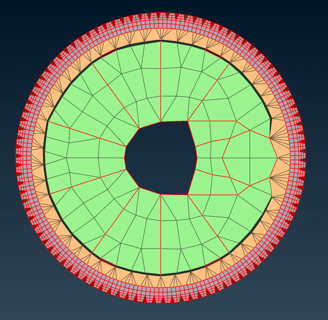
Spline gearwheel
In this section's images, a shell-solid hybrid FE model of a spline gear can be seen. This component is part of an assembly meshed with high level of details in order to obtain feature representation accuracy.
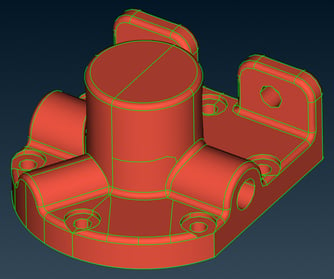
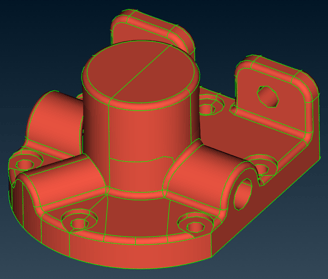
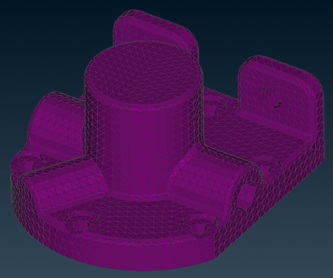
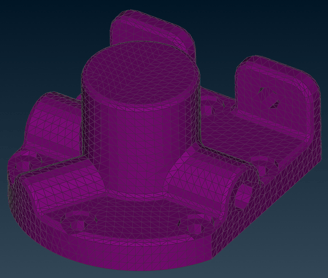
Tetra solid bracket
Building tetra solid models that closely resemble the geometry can be challenging sometimes, depending on the element length specifications or the desired element count. However, some aspects that stay the same when we are building an FE twin of a mechanical component, are as follows:
High level of attention to detail
Round features always have well defined shapes and boundaries
3D holes have even number of element rows
Radiuses/fillets are meshed in a constant-continuous manner
Features simplification does not affect real life functionality